Cast Resin Transformer
intranselectro@gmail.com
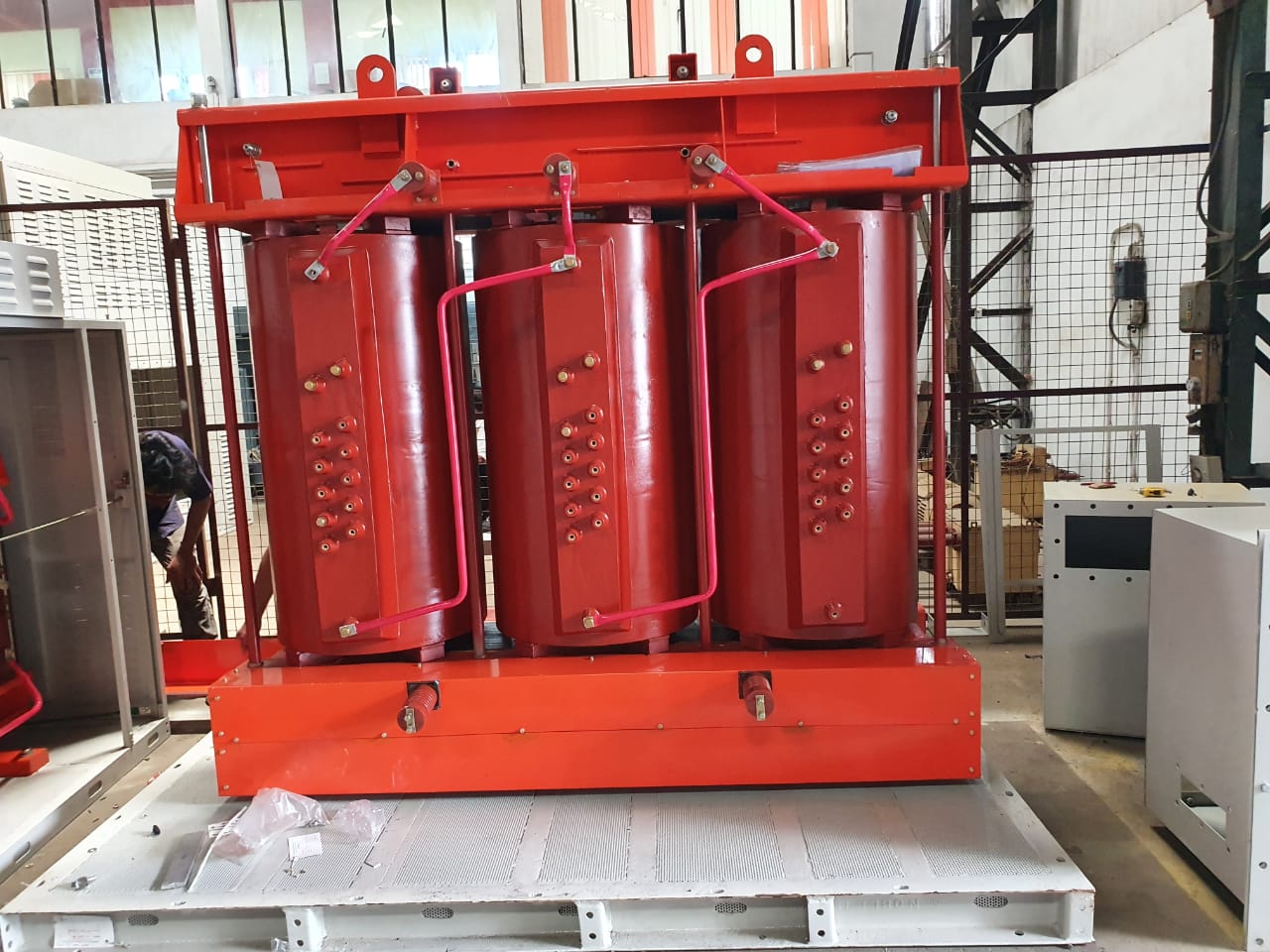
Cast Resin Transformer
We manufacture lower range of Cast Resin Transformers (CRT) both single as well as three phase, ranging from 16 KVA to 2500 KVA capacity. Our Cast Resin Transformers are designed effectively to reduce line cost and line losses and improve the quality and reliability of the electrical supply system.
The transformers can be made suitable for direct pole mounting, indoor application, hazardous area application etc. These are capable of withstanding mechanical and thermal stresses caused by short circuiting in accordance with Bureau of Indian Standards Specification 11171.
PROCESS DETAILS
Core :
Cores are made out of high grade CRGO Steel. These are cut precisely using special cutting tools to obtain burr free edges and ensure proper alignment, low core losses and low noise generation. Annealed core laminations are assembled on core frames and then clamped with suitable mechanical structures. The core edges are given a protective coating.
Coil Winding :
The high and low voltage coils are made out of fibre glass covered copper conductors. They are wound on variable speed machines. The windings are then assembled into precise moulds for the casting process.
Casting :
The mould assembly with the completed winding is first preheated and then placed into the casting vessel. The casting mix comprising resin, hardner and additives such as fillers, colour paste, accelerators and plasticisers are closed by precisely controlled pumps into a thin film degassing mixer where it is thoroughly homogenised and degassed. When the vaccum level and temperature in the casting vessel reaches the predetermined value, the resin mix is introduced into the moulds containing the active parts.
Curing :
Once the resin filling is over, the mould assembly is transferred to the Polymerising oven where controlled curing cycle is applied, so that the resin system cures without any internal cracks. After curing, the coils are demoulded, finished.
Core Coil Assembly :
The cast coils are inserted on the core limbs. Resin Cast spacer blocks, end blocks and separators are used as required. The end frames are assembled at this stage.
Tanking :
Precisely welded tanks smoothly finished and strongly built to withstand mechanical shocks and vibrations are used as protective enclosure. The core and coil assembly is lowered into the tank and then locked in position. The type of ventilation and protection offered will be different for different applications.
Testing :
Apart from section – wide testing of different assembled parts, the fully assembled transformers are tested for voltage ratio, polarity, exciting current and no load loss, impedence and load loss, seperate source high voltage test. Partial discharge measurement is done on all transformers. Special tests can be conducted as specified.
Tapping :
Generally an off circuit Tap Changer is provided to adjust the HV winding to meet the local voltage condition. Normally +/- 2.5% and +/- 5% tapping are provided on HV side. Any special requirement from customers can also be considered. On Load Tap changers (OLTC) are also provided as per customer’s requirement.
OPERATIONAL ADVANTAGE
- Resistant to short circuits (high mechanical strength).
- Non – inflamable.
- Resistant to temperature fluctuations.
- Resistant to Moisture.
- High overload capacity.
- Space saving permitting compact installation as Unitised substations.
- Practically no maintenence.
- No leakage of oil or pilferage.
- Long and trouble free service.
SPECIFICATIONS
- Power Rating : —-KVA
- Number of Phases : Three phase
- Frequency : 50 Hz
- Primary Voltages : 11,000 V
- Secondary Voltages : 433 V
- Tappings : +/ 5% to -10%in steps of 2.5%
- Impedance : 4.5% to 5.5%
- Basic Impulse Levels : 75 KVp
- Winding Material : Copper
- Applicable standards : IS 11171
FITTING AND ACCESSORIES
- Lifting lugs
- Mounting Channels.
- Rating and diagram plate.
- HV & LV bushings.
- Terminal connectors (where specified).
- Temperature sensing devices(where specified).